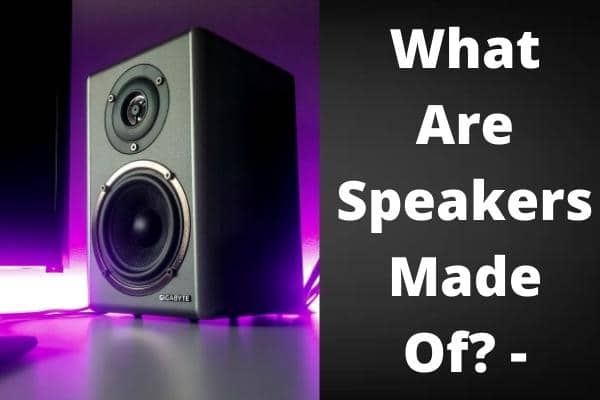
All around us are speakers. They’re in our phones, schools, venues and stages, vehicles, houses of worship, home entertainment systems, and much more. They are everywhere.
Audio speakers come in all shapes and sizes, from the tiniest in-ear devices to the massive sound systems utilized at rock concerts. Speaker configurations are all possible with stereo or mono, omnidirectional, electrostatic, active or passive, or additional options.
What are speakers made of? Speakers use an electromagnet coil, a permanent magnet, and a cone to convert electrical signals into audible sound.
The ideal material for a speaker cabinet would be extremely stiff. It would not shift with changes in the pressure in the box. When air pressure deflects it, it would also be very well damped, such that it would return to its original location without echoing.
An extremely high-frequency supersonic resonance would also prevent it from vibrating in response to lower air pressure in the box. Good-looking materials get extra points, as do those simple to cut, glue, and finish off with it.
Even if it is expensive, fantastic material will be affordable. We all have to relocate speakers at some point, and it’s impossible to enjoy decent speakers if you’ve got a painful back from doing so.
It would appear that no material is flawless in light of such characteristics. On the other hand, many materials possess many of the aforementioned positive characteristics to produce outstanding speaker cabinets. Each has its pros and disadvantages.
- What Does A Speaker Consist Of?
- Common Materials for Speaker Cones:
- What Is The Purpose Of A Speaker Magnet?
- What Is The Purpose Of Speaker Boxes?
- What Is The Finest Material To Use To Build Speaker Boxes? Why?
- 1. Chipboard:
- 2. A boulder:
- 3. Plexiglas / glass:
- 4. Wood/wood laminated:
- 5. Metal:
- 6. Lined Chipboard:
- 7. Carpentry:
- 8. Oriented strand board (OSB):
- 9. Medium Density Fiberboard (MDF):
- 10. Plywood:
- How are Speakers Built?
- Components Made of Metal
- 1. The Last Meeting
- 2. Assembled:
- How Are Speakers Made?
- 1. The first step is to build a permanent magnet.
- 2. The next build is the frame.
- 3. In the next Assembly of the Cone, Surround, and Spider:
- 4. In the next step, The Voice Coil build
- 5. Now Attaching the Magnet, Core, and Frame.
- 6. In Sixth Step Putt the Cones Together with the Frames.
- 7. The speaker housing is the final step in this process.
- What Effect Does the Material of the Speaker Cone Have on the Sound?
- 1. Paper cones:
- 2. Plastic cones:
- 3. Metal cones:
- 4. Fiber cones:
- 5. Woven composite cones:
- Quality Control:
- Compared to other materials, what are the advantages of using aluminum drivers?
- Which speaker brand is best for your needs?
- What are the characteristics of an “ideal” speaker cabinet?
- Conclusion:
- Frequently Asked Questions
What Does A Speaker Consist Of?
Manufacturing and assembly methods may vary depending on speaker type or quality level. For example, some speakers employ iron plates as the speaker cone’s foundation, while others use brass or another material. The main idea is to keep unwanted vibrations from interfering with the sound by providing a sturdy base for the plastic or cardboard cone.
Once the stiff foundation has been cut to size, it can polish on a lathe or hand until it fits the required specifications. Following this, drill pilot holes for screws or other fasteners, then add the core and attach it to its backing frame using glue and screws. Wool or foam is used to fill up voids to reduce echoes.
To produce sound, a speaker consists of the following components:
- Permanent magnet: The loudspeaker basket’s permanent magnet repels the magnetic field created by the voice coils’ use of an electrical current to power them. Various shapes and sizes are available but don’t become magnets until the last stage of the manufacturing process. Some speaker manufacturers use alnico magnets, ferrite, and lightweight neodymium.
- Voice coil and bobbin: The bobbin is a spherical tube joined to the bottom of the cone by the voice coil. The magnetic field created by an amplifier’s musical output runs via a long and tightly wound wire coil known as the voice coil.
- Spider or suspension: Wavy-shaped spider or suspension: the Spider is a woven material that helps keep the cone in place as it moves and supports the voice coil bobbin assembly
- Cone (diaphragm) & dust cap: The magnet and voice coil work together to move air and create sound through a cone-shaped rigid material called a diaphragm. A tiny piece of cloth (like a “cap”) covers the center entrance to keep dust and grime out.
- Speaker basket: When it comes to speaker pieces, the basket is the piece of metal that holds them all in place. The speaker assembly can also be mounted to a box using this method.
- Speaker terminals & braided wire: A braided wire connects the speaker wire to the speaker terminals, metal tabs, or connectors. A flexible braided wire connects to the voice coil and moves with the cone.
- Surround: Circular material, typically rubber or foam is used to link the top edge of the cone to the basket. This material is highly flexible and robust.
Common Materials for Speaker Cones:
Many materials can make the speaker cone, including plastic, paper, and Aluminum. It’s crucial to remember that each material has its own set of characteristics that affect its ability to generate sound.
Cones made of paper are the most prevalent. A mixture of wood, fibers, wax, and resin uses in making paper. The speaker’s sensitivity increases when it compresses. Because of their high sensitivity, paper cones utilize higher frequencies, such as those produced by a tweeter.
Using plastic cones is a cost-effective way to improve sound absorption. There is a risk that the sound dampening qualities will muddle the sound. The majority of low-cost speakers make from plastic.
Speaker cones made of Aluminum and other metals utilizes. Vibrations might start and stop abruptly since the metal is not liable. In general, aluminum cones have a lower frequency response than plastic cones—the speakers in toys and tiny gadgets made from Aluminum.
In order to respond to vibrations more quickly, fiber is the ideal material. The material can accurately reproduce sounds of all frequencies, from low to high.
What Is The Purpose Of A Speaker Magnet?

Permanent magnets (often ceramic or neodymium) with a narrow circular gap where the voice coil suspends and use in loudspeaker magnets. The magnet’s stable magnetic field draws or repels the voice coil.
In a sense, the coil is an electromagnet because it produces a magnetic field. Ceramic magnets are more cost-effective, despite their bigger size, than neodymium magnets, which are more robust due to their higher density of magnetic fields. Ceramic magnets are used in speaker applications because of this.
There is a hole in some at the middle, but not all, speaker magnets that help ventilate the voice coil and keep it cool.
What Is The Purpose Of Speaker Boxes?

The speaker driver’s cone creates both front and back pressure waves as it moves. The air it pushes and pulls behind it creates negative pressure as it travels closer to you, pushing air. There will be no pressure generated by either side on either side of the driver when the wavelength of a signal’s frequency is significant about its size.
As a result, low frequencies (bass) are rendered inaudible at any reasonable distance. Remove a driver from its case if you want to give this a go at home. When contrasted to how the speaker sounded when it constructs, the sound will sound “tinny.”
Keeping the pressure wave from the back of a speaker cone from canceling out the wave from the front is critical to ensuring that the speaker works at all frequencies. A similar effect can achieve by mounting the driver in a big, rigid sheet of material (a baffle).
Because a wide baffle is required to prevent low-frequency cancellation, this isn’t an option in most cases. It can do more efficiently with closed containers.
What Is The Finest Material To Use To Build Speaker Boxes? Why?
Remember that sound should only come from the speakers and the particular technological holes (phase inverter, transmission line) in the speaker enclosure. You must ensure that it doesn’t get in any other way. Making them from dense materials with a high level of sound absorption is advised.
To support the speakers, here are some samples.
1. Chipboard:

Compressed wood chips and glue uses to create these boards. The top is smooth, and the center is loose and pliable. Chipboard is a good damper of vibrations, yet it still has a distinct sound. Plates can glue together using wood glue or mounting adhesive. But their edges are prone to crumble, making it more challenging to deal with the material. It is particularly wary about moisture since it might quickly absorb and swell in the event of a breakdown in the production process.
Thicknesses ranging from 10, 12, 16, 19, and 22 mm are available from the shops. When it comes to tiny buildings (less than 10 liters), 16 mm thick chipboard will suffice, while 19 mm wide boards should use for larger structures. A film or cloth, putty, and paint can apply to the surface of the chipboard.
DN-304S speakers build-out of chipboard. Because the chipboard is acoustically inert. The speakers don’t resonate and color the sound even at high volume, so the maker picked it.
2. A boulder:
Marble, granite, and slate are the most widely utilized. A slate shell is the best option since it is easy to work with due to its structure, and it absorbs vibrations well. Some unique tools and expertise are required to process stones. You may save time and effort by cutting out simply the front surface of a stone instead of the entire thing.
The weight of a stone audio speaker (54 kg) necessitates using a mini-crane to mount the columns on a shelf. The frames themselves must be sturdy enough (for comparison, an OSB column weighs about 6 kilograms). Because of this, their cost can describe as “extremely heavy,” but the results are worth it.
Audiomasons is a company that makes columns out of a single piece of stone. The shells are made of limestone and weigh approximately 18 kg. Developers claim that even the most discerning music lovers would enjoy the sound of their device.
3. Plexiglas / glass:

You may create the speaker case out of transparent material, which is a great way to observe the “insides” of the column. It is critical to remember that the fine body won’t be clear without sufficient isolation because sound-absorbing material will cover it up.
The Crystal Cable Arabesque is an excellent example of high-end acoustic glass equipment. Crystal Cable equipment cases are manufactured in Germany using 19 mm thick glass strips with ground edges. It’s done in a vacuum unit so that there are no air bubbles in the finished product.
Updated Arabesque received all three Innovation Awards at CES 2010 in Las Vegas. No manufacturer has generated truly high-end sound using acoustics constructed from such a complicated material in the past few years. – wrote the critics. “Crystal Cable has demonstrated that this is doable.”
4. Wood/wood laminated:

A crucial element to keep in mind is that trees “breathe,” which means they expand and contract based on the relative humidity of the air.
Tension is built up in the wooden block because it glues on all four sides. It could lead to the wood splitting over time. Sound waves can’t travel through the body if it happens.
5. Metal:

As a general rule, aluminum alloys employs for these reasons. They are both light and tough. According to some experts, Aluminum can diminish resonance and facilitate the transmission of high frequencies in the sound spectrum. Aluminum has grown in popularity among audio equipment producers because of its many desirable properties and its uses in creating all-weather acoustic systems.
An all-metal body may not be the best choice, according to others. Aluminum upper and lower panels and strengthening walls, on the other hand, are worth a shot.
6. Lined Chipboard:

That is chipboard that has one or both sides covered in decorative plastics or veneers. Wood glue can use to seal wood veneer plates. However, a specific glue is needed to fill chipboard plates lined with plastic. The edge tape can use to process the board cuts.
7. Carpentry:

Laths, bars, or other fillers that are veneered or veneered on both sides are popular building materials. Low weight and easy edge processing are two advantages of the carpentry board.
8. Oriented strand board (OSB):

OSB boards make from numerous layers of thin plywood and glue. The pattern on the surface resembles a mosaic of yellow and brown colors on the surface of each board. Even though the wood texture lends this material a unique appearance, the material’s surface can be sanded and polished. This stove boasts a good sound absorption coefficient in sound absorption and vibration resistance.
OSB utilizes to create acoustic screens because of its characteristics. Create a listening area with screens. Listening to speakers at their best in almost ideal conditions Strips of OSB are arranged in a Schröder panel. A specific distance separates each strip. When an acoustic wave of the calculated length apply to a band fixed at particular spots, the band begins to radiate in antiphase and dampens it.
9. Medium Density Fiberboard (MDF):

Wood shavings and glue uses to create a smoother substance than OSB. MDF‘s structure makes it ideal for designer cases since it cuts easily. It makes it easier to combine pieces mounted together with mounting glue.
Veneer, putty, and paint can all apply to MDF. Between 10 and 22 mm in thickness, the plates are suitable for columns with volumes of up to 3 liters and a maximum of 3 kilograms; for columns with more than 10 liters, 16 mm thick plates requires. 19 mm is a preferable choice for more significant cases.
Assuming that the sound quality of a speaker enclosure is not taken into account while selecting the material. The three most important considerations are cost, processing ease, and gluing ease. MDF has all three of them. The low cost and “ductility” of MDF make it a preferred material for the production of speakers.
10. Plywood:

Thin veneers squeeze and cement together to create this substance (about 1 mm). For increased plywood strength, the veneer layers stack one on top of the other so that the wood fibers face each other. Sound can keep inside the enclosure by using plywood to reduce vibrations. Ordinary wood glue is all that is needed to join plywood boards together.
Plywood is harder to sand than MDF. Therefore you must cut out the sections as precisely as possible. Plywood’s ease of use is one of its advantages. It is because canceling a concert because the artist has a ripped back is disrespectful. Hence cases for musical instruments are commonly fashioned.
Penaudio manufactures floor acoustics with Latvian plywood, a birch-based substance. Penaudio. Treated birch plywood, varnishing after especially, has a distinctive appeal to many individuals. Penaudio’s “calling card” is a transverse layer of plywood glued together horizontally.
How are Speakers Built?
Despite the tremendous developments in component materials, the essential operation of a loudspeaker has not changed much. A permanent magnet interacts with an electromagnet (voice coil) to produce sound waves by moving a cone back and forth.
Since its establishment in 1966, Eminence has been a significant provider of loudspeakers for various industries, including professional audio, musical instruments, automobile audio, and home hi-fi systems.
Even though we’ve improved our components and production procedures, the way we put speakers together now isn’t all that different from how we did it when we first began out.
Magnets that are permanently magnetized:
The voice coil’s electric current and magnetic field attract the loudspeaker basket’s permanent magnet. These magnets are available in various sizes and materials. But until the loudspeaker assembly reaches the end of our production line, they aren’t magnets at all. Ferrite, neodymium, and alnico (a mixture of Aluminum, nickel, and cobalt) magnets use Eminence.
Components Made of Metal
The basket, top plate, rear plate, and core are all metal components used to manufacture a loudspeaker.
At Eminence, we work with a wide range of loudspeaker baskets, ranging from small to large. All of our frames make from cast Aluminum or stamped steel, and they range from a diameter of 5 inches to 18 inches. Powdered metal and steel cores are also available, ranging in size from 1″ to over 4″, in both vented and solid construction.
The Press Shop stamps the top and back plates out of steel rolls. There is around core welded or staked to the backplate of the basket, and the top plate is either welded or staked to it. The permanent magnet will sandwich between these two plates.
Metal components are assembled and then painted using our in-house e-coat technique. The metal components have a consistent coating of cationic epoxy paint applied to them at a controlled thickness of fewer than 0.001 inches.
There are no complicated parts here.
The cone, dust cap, Spider, and surround are the soft elements of a loudspeaker. Our cones come in various shapes and sizes, and the paper bodies are the most common. Foam or Santoprene can use as a backing for any of these substrates. The cone is returned to its original resting position using the mechanical suspension, consisting of the Spider and the surround.
1. The Last Meeting
Glue or rivets attach a terminal board to the painted basket/top plate assembly as the first step in the final assemblage process. A back gasket is put to the basket if the speaker is placed in the enclosure’s front.
Using a centering gauge, attach the magnet and painted backplate/core assembly to the top plate to provide a uniform magnetic gap—the small space between the permanent magnet and metalcore where the voice coil rests.
2. Assembled:
The final step is to put all the pieces together to make a speaker. Rivets or glue should join the terminal board’s top plate/basket assembly. In order to secure the speaker to the enclosure, a gasket should be applied to the basket next.
A centering gauge uses to ensure that the painted backplate/core assembly and magnet and the tight area between the magnetic core and the permanent magnet are all glued in place.
Glue bead applied to the speaker’s basket flange to help secure the cone surround. Afterward, using a vacuum, you remove any remaining debris from the magnetic gap. The next step is to attach the Spider to the basket by applying a dab of glue to the bottom of the Spider and then placing it over the voice coil. As of this stage, the voice coil has been the glue to a spider, and the Spider has the glue to a basket.
Next, the cone is put into the basket and squeezed onto the previously applied adhesive bead. The voice coil is then attached to the cone using a second bead of adhesive. Through the pre-drilled holes in the cone, wires from the coil send to the terminals, where they terminate.
Finally, the voice coil’s lead wires strengthen to cover them with rubber cement after removing the Mylar gauge.
How Are Speakers Made?
There is a lengthy manufacturing process involved in the production of speakers. It includes making the magnet, the frame, the cone, and the coil. Examine the process step-by-step.
1. The first step is to build a permanent magnet.
When making the permanent magnet, strontium and iron oxide are combined. Then, the combination is ground into a fine powder by a mill. Afterward, the powder is mixed with a ceramic binder, sealed in a metal die, and then heated in a furnace.
2. The next build is the frame.
There are two options for the speaker frame: Aluminum or steel. After the sheet creates, it delivers to a cutting machine on a conveyor. In order to cut holes in the sheet, a hydraulic press is employed. Air can flow freely from the cone as a result of this.
3. In the next Assembly of the Cone, Surround, and Spider:
The composite paper uses to create the spiders, cones, and surrounding areas. Assembled, they bond together.
4. In the next step, The Voice Coil build
Coils of copper wire wrapped around plastic are known as voice coils. A plastic spindle uses to wind numerous thin insulated copper wire turns around the voice coil. The bobbin and voice coil attach to the dust cap of the cone on top of a soft iron core. It tucks inside the basket’s entrance.
5. Now Attaching the Magnet, Core, and Frame.
Once all components have been assembled correctly, the voice coil assembly and bolting can complete successfully.
6. In Sixth Step Putt the Cones Together with the Frames.
The cone assembly is joined to the frame assembly once completed. To begin, glue the Spider to the frame’s bottom. Afterward, the surround nails to the frame’s top. Spiders and rubber surround fasten separately. However, this isn’t a rule.
7. The speaker housing is the final step in this process.
Focusing sound signals produced during operation are made more accessible by the speaker’s housing material. Because of this, the speaker encases in a box. Different materials and forms can use to make speaker enclosures.
Speaker enclosures are typically crafted with medium density fiberboards (MDF) to dampen and stabilize the speaker’s vibrations, making them more stable and reducing unwanted noise.
Portable radios, for example, use plastic or Aluminum for their built-in speakers. Plastic is more cost-effective and is the most common material. Aluminum, despite its affordability, is less likely to protect speakers from vibrations and is less frequently utilized.
What Effect Does the Material of the Speaker Cone Have on the Sound?
It is the speaker cone’s vibrations that give speakers their sound. When it comes to how a cone works, there’s a lot of science at play. Speaker cones can make from a variety of materials. Paper, plastic, fabric, and metal are all examples of these materials.
Speaker performance influences the cone material used. The question of which cone material works best will never settle. Certain qualities make one material better than the other. Understanding how speaker diaphragms work and their impact on the sound quality is critical.
1. Paper cones:
In terms of cost, paper is one of the most accessible materials. The majority of early speakers used paper cones. Paper is a lightweight substance that can easily follow the coil’s motions. Using paper to make enormous speaker cones is a cost-effective option. In absorbing water, the paper expands in volume and changes in damping properties. Because they are from paper, paper cones break easily when under pressure. As a result, they can puncture quite readily.
Basically, paper cones are formed of a mixture of wood, wool, and felt, among other things. It is also possible to add various chemicals to the paper compositions to improve their durability and make them more suitable for speaker cones. It means that paper cones can produce out of multiple materials.
During the production process, paper speaker cones can be pressed or unpressed. The larger surface area of non-pressed cones allows them to push more air, resulting in a louder sound.
As a result, non-pressurized paper cones are more power-efficient. Non-pressed paper, on the other hand, has been chemically treated to become more rigid. On the other hand, Pressed paper cones have a lower surface area. But claim to have fewer quality difficulties than non-pressed paper cones.
2. Plastic cones:
Another type of cone makes from plastic. Plastic is preferable to paper because it is more brutal and durable. Cones can make from a variety of plastics. Polystyrene, a kind of plastic, was utilized to build speaker cones in the early days of flat-panel speakers. Polystyrene becomes loud and intrusive when flexing. Hence its use restricts.
Polypropylene is the most popular material used to make cones nowadays. In terms of deformation and moisture absorption, polypropylene is a good choice. Such speakers might be in a restroom, a ceiling or wall speaker, or a home theatre system.
Polypropylene is an excellent material for producing most cones because of its unique properties. As a result, it’s a solid foundation, dependable, and well-distributed. The production process makes easier because polypropylene is pliable and easy to deal with. Moisture-resistant, it resists mold and mildew. On the other hand, paper cones are prone to tears and punctures more easily.
In addition to its lightweight, polypropylene chooses over other plastics. As a result, it can move with the coil’s vibrations. In addition, it offers insulating qualities for electronic devices. It prevents other speaker locations from receiving current. When flexed, polypropylene can produce a lot of noise.
3. Metal cones:
Aluminum and Magnesium are the most frequent metals used to make speaker diaphragms. In terms of color and distortion, metal is the least affected by other materials.
Metal, on the other hand, has weak damping capabilities. Woofer cones made of Aluminum are ordinary. In terms of weight and stiffness, Aluminum and Magnesium are nearly identical.
Compared to Aluminum, Magnesium has a lower dampening capacity. On the other hand, Aluminum is both inexpensive and easy to deal with.
Metal cones, which are incredibly strong and long-lasting, can flex and ring. The quality of sound degrades by ringing. However, enhancing the damping qualities of metal by doping it with chemicals might lead to performance concerns.
4. Fiber cones:
Carbon fiber and Kevlar are among the most prevalent fiber materials in cones. In the majority of woofer drivers, carbon fiber is employed. Despite its small size, it’s highly durable and long-lasting.
It’s also durable and adaptable, allowing it to produce a large amount of work. The most common usage of carbon fiber is as part of composite materials that are molded or woven. Paper cones can also be covered in it to increase the strength of the paper.
Carbon fiber is difficult to work with because of its unique properties. Consequently, it utilizes other materials rather than single components.
Kevlar makes from synthetic fibers. Bulletproof vests are an everyday use for this material. Speaker diaphragms can also make from Kevlar. When producing cones, they weave and shape. It is possible to coat kevlar with other materials and utilize it to produce cones.
Although Kevlar is robust and lightweight, its lack of dampening characteristics causes it to ring like a bell. Some frequencies cannot be exhausted because of this. Because of this, it is frequently used with other materials to achieve better effects.
5. Woven composite cones:
Speaker manufacturers are continually attempting to develop the most excellent cone material. The advancement of woven composites has led to the creation of superior cones. Woven cones can make using a variety of methods.
Glass, carbon fiber, and aramid fibers dominate the composition of woven cones. Different types of resin-treated woven sheets are available.
Fibers woven in this way are perfect for cones because they are light and rigid. Epoxy seal coating makes woven fibers heavier, making them less suitable than paper or plastic cones.
So some fibers are coated with polypropylene so that they retain their lightness. Unlike paper and polypropylene, Woven fibers tend to be more expensive and difficult to get, making them less suitable for mass production.
Quality Control:
Inspectors also check the speaker’s manufacturing process after it builds. Cracks and defects in the permanent magnet are inspected at this step. Additionally, the paper cones are checked for holes or faults in the material and adequately glued.
For this reason, the entire speaker assembly examines quality and adherence to standards. It is then linked to an audio generator to test its frequency response and power. That is the final step to confirm that the speaker reproduces sound following requirements.
Compared to other materials, what are the advantages of using aluminum drivers?
The intended use dictates the best cone material selection. For every application, not every material is the best fit. Aluminum is a good choice for the bass driver in cost and performance. The stiffness-to-weight ratio is excellent, and it is easy to create. More exotic materials have little or no advantage in this bass driver size.
It is common for midrange drivers to make materials that are not stiff throughout their operating range. Aramid fiber, for example, is used in the Debut speaker series. It allows us to fine-tune the flexing of the cone to achieve the most outstanding results.
Additionally, we can now use a three-way speaker to alleviate some design challenges associated with eliminating flexing in the operating range. Aluminum achieves exceptional performance with its first flexure mode at a high 8kHz in the Uni-Fi midrange.
Which speaker brand is best for your needs?
There are various elements to consider when choosing a speaker brand, including your budget, the size of the area you have, and the features you want. Don’t just buy something because it says “best”; conduct some research beforehand to ensure it’s the most excellent choice for you!
Setting a budget is one of the most crucial things to do. How much are you prepared to spend? This list isn’t complete, so make sure that your purchase will fit your needs in terms of features and price point before making your final decision.
Next, think about the size of the area you’re working in. How much floor area do you have available?? Bookshelves are also an issue. Buying a sound system that won’t fit in your house is a bad idea!
It’s also important to consider whether or not you want options like Bluetooth (wireless music streaming), audio input/outputs, etc., in your new speaker. Make a list of everything you need and want, and you’ll be sure to find a solution.
As the last step, reading customer reviews may be pretty helpful in determining which speaker brands have satisfied consumers and manufacture high-quality products.
What are the characteristics of an “ideal” speaker cabinet?
Sound from a loudspeaker driver amplifies more effectively when the enclosure it is housed in exhibits little distortion. A loudspeaker’s enclosure is as crucial to its design as the driver itself. Materials and design are equally important in determining the performance of a speaker. To be a great speaker, you need to use:
- If you don’t want to hear distinct sounds or lose energy at specific frequencies because of vibrations or mechanical pressure, solid (or heavy) materials should be used.
- The more rigid a cabinet is, the more efficient it is and the less prone to distortion.
- When knocked, something that makes a ‘dead’ sound is said to be non-resonant. On the other hand, metal is the material of choice for making bells and tuning forks. Your music will distort if you hear ringing sounds.
Conclusion:
When it comes to making cones, the most excellent material doesn’t bend. It should have the most efficient piston action possible. Choosing an effectively dampened, lightweight, and rigid material is also essential. It should start and stop vibrating with the touch of a button.
It’s essential to have a material that can precisely reproduce sound impulses while minimizing distortion. A single material, however, does not exist. Even though the ideal material should be lightweight and stiff, more rigid materials are heavier, and less rigid ones are lighter. In order to build low and high-frequency drivers, many materials can use.
Only a few materials can use to make low and high-frequency drivers. As a result, designers choose nearly perfect materials but have minor flaws for specific uses. Material that reproduces voice coil signals accurately and with the least amount of distortion is the primary goal when selecting a speaker cone material.
So the optimum material maintains tight mobility and increases the frequency breakup point. Because of this, producers are looking for new ways to combine the desired features of cones made from composite materials.
We hope that now your search for What Are Speakers Made Of? ends here!
Frequently Asked Questions
Are you looking for the best material for a speech?
As far as materials go, concrete is the most excellent option for creating speakers. As you can see above, it can mold into a wide variety of shapes.
How are Bluetooth speakers constructed?
The majority of low-cost speakers make of plastic. Speaker cones made of Aluminum and other metals utilizes. Vibrations might start and stop abruptly since the metal is not liable. In general, aluminum cones have a lower frequency response than plastic cones.
How are Bluetooth speakers constructed?
Paper, metal, plastic, and aramid fiber are all common materials for speaker cones. Sound qualities, advantages, and downsides are unique to each material.
To make a Bluetooth speaker, what do you need to have?
An RF receiver integrates within the loudspeaker’s main speaker unit, which also houses the loudspeaker itself. Wi-Fi equipment, televisions, PCs, MP3 players, and other audio devices can connect to the transmitter.
What is the material used to create wireless speakers?
Frame, magnet, iron core, and voice coil are only a few parts that make up the speaker system. The magnet and the cone are affixed to the structure. When the voice coil connects to any audio source, it is an insulated wire wrapped around the bobbin. Iron forms the core of this bobbin, which mount on an iron cone for easy assembly.